Why is Consulting Required for Quality Management Systems?
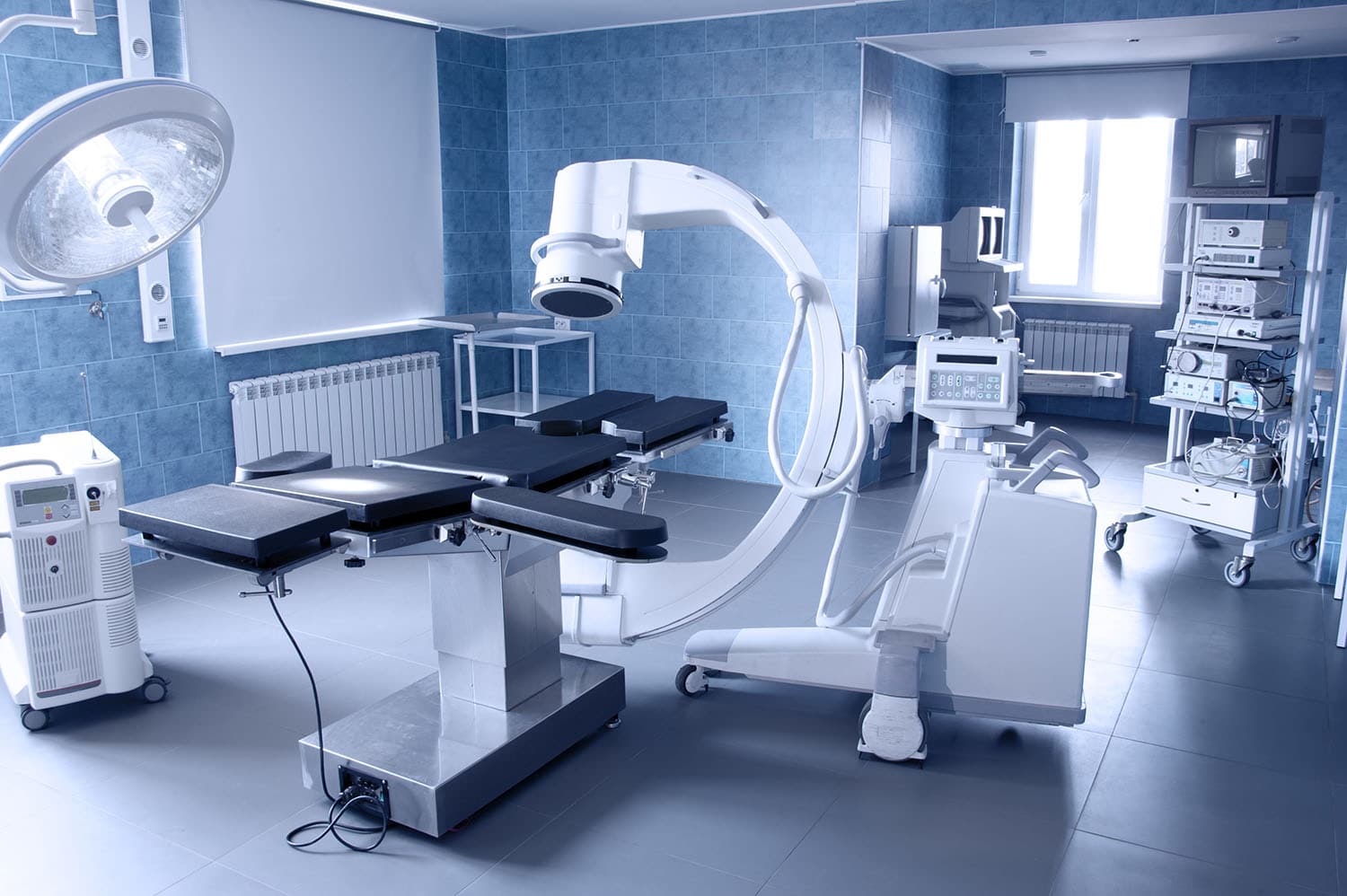
Quality Management System Consulting is the practice of assisting small, medium and large
- All facilities engaged in the production of primary packaging materials for medicinal products require a Quality Management System (QMS) for ISO 13485 certification. Developing a comprehensive system to meet all the requirements of ISO 13485 for effective implementation to achieve desired results, a competent ISO 13485 consulting company or a competent ISO 13485 consultant is essential
- ISO 13485 consulting companies assure required QMS is developed to comply with all customers and regulatory requirements and the organization can demonstrate that the facility has a robust system and can produce quality products and ensure safety for consumers
- ISO13485: 2017 is an international standard dedicated to build QMS for primary packaging of medicinal products and pave way for continual improvement in any facility
- A competent ISO 13485 consulting company or ISO 13485 consultant can provide detailed explanation on the intent of the standard while developing an ISO 13485 compliant Quality Management System(QMS)
- A comprehensive QMS can create confidence in end users, government, statutory and regulatory agencies and provide answers to all questions from Regulatory and Certification Body Auditors
- An ISO 13485 consulting firm provides the techniques for developing and implementing the QMS
- A consulting firm can provide internal auditing services to effectively conduct ISO 13485 conformity audits to fully prepare for ISO 13485 certification audits to ensure implementation
- ISO 13485 consulting companies or ISO 13485 consultants can minimize FDA audits and product recalls through robust compliant system development and effective implementation techniques
3rd Party audit Certification Bodies (Accredited by International Accreditation Forum =IAF) perform the audits on the organizations to grant ISO 9001 Certifications with demonstrated evidence of conformity to all the requirements of ISO 9001:2015.
- The certification is renewable every three years
Benefits of Having an QMS for Medical Devices:
The benefits of implementing ISO 13485:2016 management systems are diverse and will be seen in all departments of your company. The following are some of the benefits that you should take into consideration:
- ISO 13485:2016 allows your organization to meet the customer requirements in the production of medical equipment.
- Provides necessary ideas to standardize quality management in the medical equipment fields.
- Certification will reduce or eliminates FDA audits
- Well built QMS for medical devices help avoid the need to recall medical devices
- Well-built ISO 13485:2016 QMS shows the way to adhere to all statutory and regulatory requirements associated with medical devices.
- Certified ISO 13485:2016 companies produce good quality medical devices which help extend human or animal life expectancy
- Critical in providing a competitive edge for your organization
What is 3rd Party Quality Audit and Consulting:
Quality Management Consultants can assist your facility to prepare for ISO 13485 certification with a simplified documented Quality Management System (QMS) and associated documents/records to be able show evidence once the system is fully implemented for the standard ISO 13485 certification for Medical Devices Class I, II, or III.
Each facility needs to prepare documentation to show as evidence of having streamlined processes that ensure Quality in manufacture and supply of packaging materials for medicinal products. An example is, documentation required to show the evidence on cleaning and sterilization preserved on medicinal products with the use of microbial free manufacture and supply of packaging of medicinal products.
Differentiation in documentation between primary packaging medicinal products with human or animal contact versus those which do not have contact. It is acceptable that no facility/company likes to produce a bad quality product or service but without an established Quality Management System(QMS), it is difficult to prevent quality wastage and contribute to the hygiene of end-user. It is, therefore, necessary to build a robust system which compels task performers to have defined roles, responsibilities and controls to ensure quality for medicinal products.
In addition to having a system, the ISO 13485 certified system is to be audited periodically to ensure that designed systems are being implemented and controls are being exercised.
The audits performed by a team from within the organization are called 1st Party Audits. Audits performed by ISO 13485 consulting companies or ISO consultants like Quality Systems Enhancement are known as a second party audits. Audits conducted by Certification Bodies are known as 3rd party audits.
All Certification Bodies are accredited through international Accreditation Forum (IAF) through Multilateral Agreements (MLA). 3rd Party audit is conducted by Accredited Certification Bodies who are signatories to IAF and MLA affiliated to ISO.
QSE Difference in Audit & Consulting Services:
- Quality Systems Enhancement Inc. (QSE) is a Premier Consulting, Auditing and Training firm engaged in the field of ISO 13485 certification to international standards
- QSE has a unique 10 steps disciplined path for ISO 13485 certification which is insensitive to failure
- QSE has assisted over 700 facilities achieve ISO certifications
- QSE’s unique document simplification tools result in smooth implementation to achieve ISO 13485 certification
- QSE identifies all processes from “Quote to Cash” in other words all activities from submission of quote, processing of the order, quality control, dispatch to customer and receive cash. All manufacturing and non-manufacturing processes are covered
- QSE’ s documentation covers all requirements of customers and other interested parties, statutory and regulatory requirements
- QSE’s unique simplified documented system is easy to integrate to other management systems
- QSE engages qualified and competent auditors to conduct internal audits
- QSE’s internal audits are more stringent than Certification Bodies audits and will help companies pass certification audits with minimum nonconformities or no nonconformity
- 98% of QSE assisted facilities passed the initial certification audit with zero deficiencies with a 100% passing rate first time around
- QSE covers all the requirements of the standard including the implicit intent of the standard
- QSE’s system development involves all relevant employees which lead to effective implementation
- QSE’s Document Simplification is unique comprehensive single level documentation which ensures effective implementation
- QSE’s documentation is unique, simple, lean and easy to implement and sustains certification audits in the long run
- QSE’s ISO 13485 internal auditing services promote the unbiased assessment of QMS implementation and the extent of implementation
- QSE ensures to provide implementation assistance or complete understanding of the documentation and requirements
- QSE’s unique management review format results in to no nonconformities against management review during certification audits
- QSE does not simply tell our customers what to do but assists them on how to do
- QSE’s 10-step disciplined path for ISO 13485 certification achieves organizations certification in the shortest possible time. Usually within 5 months
QSE provides post auditing services if required and can take the disputes to the highest levels for resolution
About ISO 13485:2016 | Quality Management Practices in the Medical Devices Sector
The ISO 13485 is a standard measure that is like ISO 9001:2008 but simply acts as a criterion to measure best management practices in the health sector. This International Standard specifies requirements for a quality management system that can be used by an organization for the design and development, production, installation and servicing of medical devices, and the design, development, and provision of related services. The certification provides a different kind of approach in the manufacture and distribution of medical equipment and there is no doubt that many medical practitioners have preferred equipment from providers and producers who have been certified by the ISO 13485. The standardization criteria is a global initiative that aims at creating a professional medical equipment production through world class management practices that are all within the ISO 13485:2016 charter.
The rational that is taken in the audit for compliance involves manufacturing and distribution of medical equipment, as well as considering the potential risk that is involved in their use. The certification allows medical equipment manufacturers to meet global standards of safety in developed countries and comply with the existing legislation in those nations. The standard initiates management systems to analyze the production of medical equipment and to come up with instructions on how to strengthen weaknesses in the system.
The requirements for ISO 13485:2016 certification are very basic and all aim at promoting high safety standards in the production and distribution of medical equipment.
Among the basic and fundamental requirements, the following are the most significant ones:
- ISO 13485:2016 requires that organizations develop and establish a quality medical equipment management practice and system in all sectors of production and distribution
- Calls for organizations to conduct comprehensive assessments of their production system to determine the strengths and weaknesses of their existing management system and further move on to develop possible solutions in regard to their findings
- Requires detailed presentation of the organization management system in order to make sure that all needs have been taken into close consideration
- The standardized measure also requires companies to implement and evaluate an internationally recognized quality management system in the production of their medical equipment
- Maintain and evaluate your medical equipment management system, documentation of procedures as well as development of an effective manual
- Promotes proper documentation of medical service and equipment management practices
Testimonials
What our customers say about us
LC Norcross, GA