Lean Management - Efficient ways to increase profit margins
One of the most efficient ways to increase profit margins in your organization is by reducing process waste. This increase of margins can be achieved through the QSE (Quality Systems Enhancement) tools which serve as a guide to help you implement the Lean Tool application concepts and practices in your working environment. By correctly implementing these tools, it will help in reducing waste of time and resources. The focus of process is on: Decreasing waste, increasing efficiency and using practical methods to decide what matters rather than using ineffective methods already in use. Our set of tools are geared towards identifying and progressively doing away with waste which improves quality. Lean is a method of making the flow better or reducing work and thus, maintaining a consistent elimination through the system. Its primary focus is on coordination by getting the rights things, at the right place, in the right quantity, to obtain a smooth-running workflow while minimizing waste. While at the same time, the process is flexible and easily able to make changes.
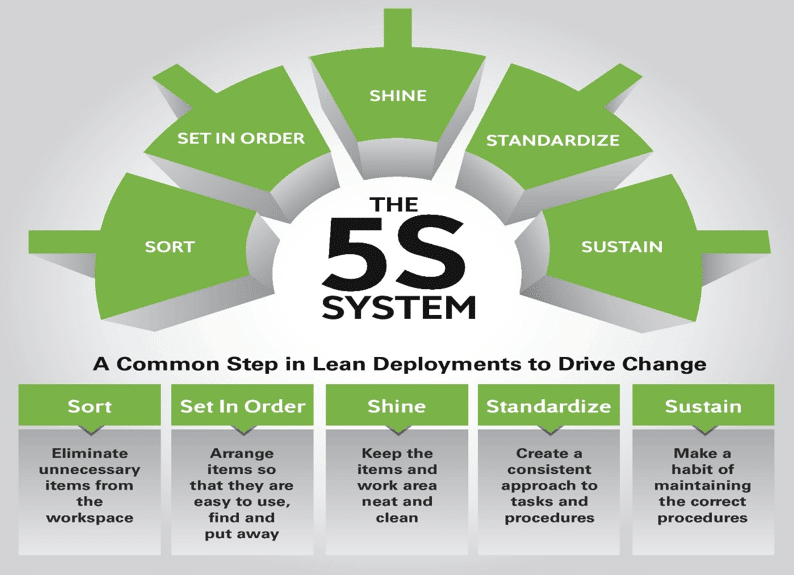
Tools used for Lean Management:
- Training on What is “Lean Manufacturing?”
- Identifying the forms of waste – 5S
- Visual Stream Mapping
- Balance Score Card
- Kanban
- Kaizen
- Visual Workplace
- Mistake Proofing (Poka-Yoke)
- Lean tools and concepts training
- Baseline assessment and establishment of goals and metrics
- Selection of appropriate lean tools and concepts
- Application of the selected tools and concepts
- Monitor improvements against goals
- Fine-tuning of processes to achieve value-added results
- Methods to Maximize/optimize implementation effectiveness for bottom line improvement
- Incorporate results into standardized procedures
- Management review of accomplished results
- Reduce the overall “Quotation to Cash” time
- Identification of areas for “error proofing”
- Increase efficiency while reducing waste and cost
- Remove unnecessary tasks
- Increased Output
- Lower levels of inventory
- Fewer Machine and Process Breakdowns
- Trained work force on Lean Management
- Training includes Statistical methods for Problem solving and process control
- Training Includes Project Management Techniques
- Cost savings justify costs towards training and implementation
- Companies that would want to get rid of wastes in their labor, defects, unnecessary human motion, inventory, transportation, overproduction and space
- Companies that want to improve or boost their employee morale should pursue Lean Manufacturing methodology
- Companies or businesses that seek to acquire an enhanced overall manufacturing flexibility.
- Businesses or companies that intend to reduce their inventory by producing only what is needed in their next operation
- Companies that want to ensure that in their production there is improved quality and fewer defects
- Creation of a safer working environment.
- Motivation of employees, which in turn enhances better production.
- Ensuring of an inventory reduction
- Improvement in methods of working
- Improvement in profitability
- A great marketing Tool
This process will be accomplished by QSE’s proven 10 Step Approach
- Lean tools and concepts training.
- Baseline assessment and establishment of goals and metrics.
- Selection of appropriate lean tools and concepts.
- Train the implementation team for the application of the selected tools and concepts.
- Assist in the application of the selected tools and concepts.
- Monitor improvements against goals.
- Fine-tuning of processes to achieve value-added results.
- Maximize/optimize implementation effectiveness for bottom line improvement.
- Incorporate results into standardized procedures.
- Management review of accomplished results.
By leveraging vast experience, it has, QSE organizes the entire implementation process for Lean Management
Lean Tools, Concepts, and Training
QSE provides comprehensive training in Lean involves which involves a 5 step Path
- Seiri or Sort
- Seiton or Set in order
- Seiso or Shine
- Seiketsu or Standardize
- Shitsuke or Sustain
Lean Gurus are now advocating for one more `S’ that is `Safety’
- 5S Seiri, or in English; Sort, Clearing, Classify. In this stage, QSE removes all clutter and unwanted items leaving only the tools, equipment, components, and machines that are required daily.
- 5S Seiton, or in English; Straighten, Simplify, Set- in-order, Configure. This stage is where QSE organizes all the remaining items; using ergonomic principles to locate items where they minimize movement and reduce stress. QSE also ensures that items are clearly identified and have a clearly identified home – “A place for everything, and everything in its place.”
- 5S Seiso, or in English; Sweep, Shine, Scrub, Clean and Check. This is the cleaning and painting of the area to bring it to a “new” standard. The reason for this is not just to make the area look pretty but to ensure that things like leaks and other issues stand out against the otherwise clean area.
- 5S Seiketsu, or in English; Standardize, stabilize, Conformity. During this phase of 6S QSE standardizes the previous stages of the implementation by ensuring common color codes and ways of working.
- 5S Shitsuke, or in English; Sustain, self-discipline, custom and practice. This is where QSE tries to make the process part of the culture of the company to ensure the ongoing implementation and improvement of this initiative.
- The 6th “S”; Safety, QSE now concentrates on safety aspects of our initiative, reviewing every action and each area to ensure that QSE has not overlooked any potential hazards.
Baseline assessment and establishment of goals and metrics
QSE consultants advise on how to record:
The current state of affairs in the organization
The Goals to which the organization can reach based on practical possibilities
The methods which will be used to measure achievement in reaching set goals
- Selection of appropriate lean tools and concepts
QSE will ensure proper tools as applicable to the organization are selected from the following tools
- Kanban
- Kaizen
- Poka-Yoke
- Visual Workplace
- 6 S
- Train the implementation team for the application of the selected tools and concepts
QSE undertakes to train select teams on the above referred tools and practically shows how the tools are applicable in daily routine
- Assist in the application of the selected tools and concepts
QSE will advise on how to apply the tools and gather data to build an evidence based system for analysis
- Monitor improvements against goals.
QSE helps organizations to come up with data to compare the base line data with data with improved methods through application of Lean tools.
Data will serve as demonstrated evidence of improvement against goals
- Fine-tuning of processes to achieve value-added results
Processes that have been affected by the application of Lean tools are now to be fine-tuned to have repeatability and reproducibility as per desired goals.
- Maximize/optimize implementation effectiveness for bottom line improvement.
Results of fine-tuned processes are now analyzed to help maximize improvements to achieve improvement in Bottom-Line, through reduction in 7 types of possible wastes in any organization
- Incorporate results into standardized procedures
Once maximized results are achieved the process parameters are recorded and incorporated in to standardized work instructions or as changes to ERP system to ensure continuation of similar processes for future use
- Management review of accomplished results.
QSE will provide all kinds of support in making presentation to Management on achievements by the teams, identifying the great contributors to the success of the projects and make recommendation to the Management to recognize the efforts in a manner which befits the organization to keep up the morale of the contributors.